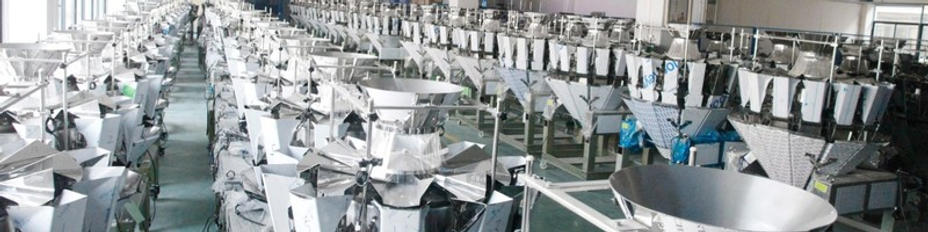
Our Services
Discover Our Full Spectrum Of Services That Are Aligned With Our Values.
- Packaging Made Easier -
Installation & Commissioning
Our team is involved in preparing the site and assembling the machine components according to technical guidelines, ensuring integration with existing production lines. This includes performing initial tests, calibrations, troubleshooting, and validating the machine to meet performance and regulatory standards. Additionally, it involves training operators and maintenance staff on proper usage and upkeep, as well as creating detailed documentation of the installation process and any modifications made.
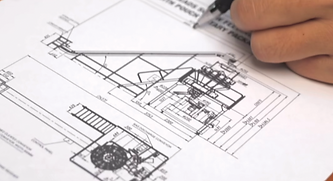
Product Training & Demo Tutorial
At Kalvac, our technical team will provide operators with our product safety procedures, routine maintenance, and troubleshooting. This includes conducting hands-on training sessions, providing step-by-step tutorials, creating user manuals, and offering ongoing support to ensure that the personnel can operate the machinery efficiently and address common issues independently. Effective training maximizes machine's performance and longevity, minimizing downtime and maintaining production quality.
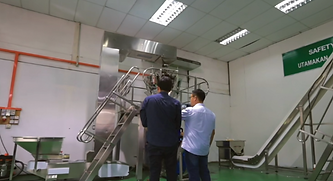
Upgrades & Retrofits
At Kalvac, we are rentlessly updating or enhancing existing machinery to improve performance, efficiency, and compliance with new standards. This process includes assessing the current machine's condition, identifying components that need replacement or enhancement, and installing new parts or software. Retrofits might involve adding new features, improving automation, or integrating advanced technologies. Upgrades ensure that the packaging machines remain competitive, meet evolving industry requirements, and extend their operational lifespan, providing better productivity and cost-effectiveness for our customers.

Preventive Maintenance
By identifying and addressing potential issues before they escalate, preventive maintenance helps maintain high productivity, reduce downtime, and minimize repair costs, ensuring the packaging machine operates efficiently and reliably. Kalvac’s team of experts offers advices and assistances involving scheduled and proactive servicing to ensure optimal performance, extend the equipment's lifespan, and prevent unexpected breakdowns. This includes regular inspections, cleaning, lubrication, calibration, and replacement of worn-out parts.

On Site Support
On-site support for packaging machines involves providing direct, in-person assistance at the customer's location to address and resolve issues that cannot be managed remotely. On-site support also includes additional training sessions for operators, implementing retrofits and upgrades, and offering tailored solutions to specific production challenges. This hands-on service ensures minimal downtime, enhances machine performance, and provides customers with personalized, immediate technical assistance.
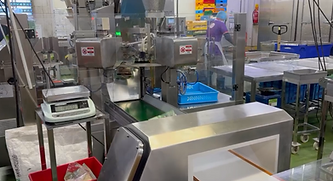
Customer Support Hotline
Our dedicated customer service team members can cater immediate assistance to clients facing technical issues or needing guidance with their machines. This service includes troubleshooting problems over the phone, offering solutions or adjustments, scheduling on-site visits if necessary, and answering any questions related to machine operation, maintenance, and performance. A dedicated support hotline ensures that customers have access to expert help to ensure efficient production processes.

Warranty Services
Kalvac packaging machines are covered with comprehensive after-sales services which include repair, replacement, or maintenance of the equipment, generally within 1 year from the date of purchase, at no additional cost to the customer. Warranty services typically involve technical support via phone or email, on-site repairs, and supply of necessary parts. Additionally, customers are often provided with clear guidelines on the terms and conditions of the warranty, what is covered, and how to request service, ensuring transparency and customer satisfaction.
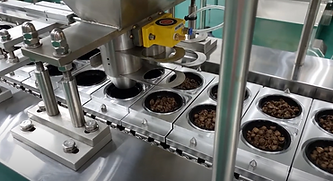
Custom Solutions
Kalvac offers custom solutions involving designing and modifying some of our products to address the unique needs of each customer. This process begins with assessing product specifications, production goals, and operational workflows. Machines can be adapted for various product types, packaging materials, and production scales, ensuring flexibility. Additionally, packaging systems can incorporate designs to minimize waste, such as using a different type of packing methods, offering clients sustainable and cost-effective solutions tailored to each and every specific business requirements of our clients.
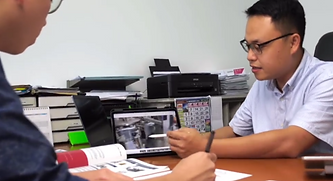
